碳酸钡振动流化床干燥机、碳酸钡专用干燥设备生产线
- 价格: ¥300000/台
- 发布日期: 2025-04-15
- 更新日期: 2025-08-30
产品详请
外型尺寸 |
1
|
货号 |
001
|
品牌 |
盛昱干燥
|
用途 |
物料干燥
|
型号 |
00001
|
制造商 |
盛昱
|
是否进口 |
否
|
专业源于专注,我们深耕干燥领域,在多个应用行业展现实力。凭借丰富的行业经验与专业技术,为不同领域客户量身打造专属干燥方案[碳酸钡振动流化床干燥机、碳酸钡专用干燥设备生产线],用专业成就客户的每一份信任。在食品行业,我们采用温和干燥工艺, 尽可能保留食材的营养成分与风味;在化工领域,针对各类化学原料,我们研发出耐腐蚀、防爆型干燥设备,保障安全生产;在制药行业,严格遵循 GMP 标准,实现药品原料的无菌、精准干燥。当传统干燥技术在复杂工艺需求前渐露疲态,您需要的是一场打破常规的干燥革命。尊贵的您,诚盼来电 [153干燥8008设备8370烘干机],一同踏上这场颠覆传统的干燥创新征程,重塑工业生产的价值坐标就在盛昱干燥 。
一、碳酸钡振动流化床干燥机、碳酸钡专用干燥设备生产线物料特性与核心技术需求
(一)碳酸钡干燥特性
- 化学性质
- 分子式 BaCO?,分解温度≥1340℃,干燥过程无需担心热分解,但需控制温度≤150℃以避免结晶水(如有)过度蒸发导致晶型变化;
- 吸湿性中等(含水率通常 10%-25%),粉末状碳酸钡易产生静电吸附,导致颗粒团聚,需低应力流化与防静电设计。
- 物理特性
- 密度 4.43g/cm3,颗粒流动性较好(安息角 30°-35°),临界流化速度 2.0-3.0m/s;
- 目标含水率≤0.3%,杂质引入量≤0.01%(避免铁、钠等金属离子污染),破碎率≤1%(保护颗粒完整性)。
(二)关键技术痛点
- 高效流化:高密度颗粒需足够风速驱动,同时避免过度流化导致能耗增加;
- 防静电团聚:粉末状碳酸钡易因静电吸附形成软团聚,需表面改性或防静电处理;
- 粉尘控制:碳酸钡粉尘有毒(LD50 418mg/kg),排放浓度需≤5mg/m3,远超常规粉尘排放标准。
二、碳酸钡振动流化床干燥机、碳酸钡专用干燥设备生产线设备核心设计与材料选型
(一)耐磨抗静电结构
- 流化床主体
- 材料配置:主体采用 SUS304 不锈钢(厚度 8-12mm),内壁电解抛光(Ra≤0.8μm)减少粉尘粘附;
- 分布板:激光冲孔板(孔径 3-5mm,开孔率 20%-25%),按等边三角形排列,板下设置导流锥(锥角 60°),使截面风速均匀度≥95%,防止局部死床。
- 振动系统
- 驱动方案:双振动电机(功率 3.0-5.5kW×2)搭配钢制弹簧(刚度系数 100-200N/mm),振动频率 16-20Hz,振幅 2-4mm(根据粒度调整,微米级取高振幅,纳米级取低振幅),颗粒抛射高度≤100mm,破碎率≤0.8%;
- 防静电设计:电机外壳、流化床体通过铜编织带接地(接地电阻≤4Ω),振动电机轴承使用导电润滑脂(型号:KLUBER ISOFLEX TOPAS L 32 N),消除静电积累风险。
(二)节能加热系统
- 热源选择
- 蒸汽间接加热(主流方案):采用翅片式换热器(换热面积 50-100㎡),蒸汽压力 0.6-1.0MPa(温度 160-180℃),进风温度控制在 120-140℃(波动 ±2℃),适用于含水率≥15% 的碳酸钡;
- 余热回收:干燥尾气经热管式换热器预热新风(节能率 25%-30%),剩余热量用于预热湿物料输送管道(温度提升 15-20℃)。
- 温度控制
- 沿床长布置 4 组热电偶(精度 ±1℃),通过 PID 算法动态调节蒸汽流量,响应时间≤15 秒;
- 冷却段采用风冷(风量占比 20%),将出料温度降至≤50℃,防止后续输送过程中粉尘粘结。
三、碳酸钡振动流化床干燥机、碳酸钡专用干燥设备生产线防团聚与粉尘控制工艺
(一)流化工艺参数优化
参数类型 | 控制范围 | 技术目标 | 调节方式 |
进风温度 | 120-140℃ | 高效蒸发水分且避免晶型变化 | 蒸汽流量比例阀 + PID |
流化风速 | 2.5-3.5m/s | 临界流化速度 1.2-1.3 倍 | 风机变频器 + 风门联动 |
停留时间 | 10-20 分钟 | 含水率从 20% 降至≤0.3% | 进料速度与堰板高度耦合 |
振动频率 / 振幅 | 16-20Hz/2-4mm | 低应力分散(纳米级取 18Hz/2mm) | 振动电机变频控制 |
床层高度 | 400-600mm | 高密度物料稳定流化 | 溢流堰高度电动调节 |
(二)防静电与分散技术
- 表面改性辅助(可选)
- 对纳米级碳酸钡(≤100nm),在预热段通过二流体雾化喷嘴喷洒硬脂酸乙醇溶液(浓度 0.5%-1%),雾化粒径≤50μm,喷量 0.2-0.8L/min,降低颗粒表面静电吸附力,团聚率从 30% 降至 10% 以下;
- 物料中添加 0.1%-0.3% 的导电碳黑(电阻率≤10Ω?cm),提升整体导电性,减少静电积累。
- 气流分布强化
- 分布板开孔率从入口端 20% 渐变至出口端 25%,形成风速梯度(入口端 3.0m/s→出口端 2.5m/s),使物料在床层内呈 "活塞式" 流动,减少返混导致的团聚;
- 流化床顶部设置导流挡板(高度 100mm,倾角 45°),抑制腾涌现象,提升流化稳定性。
四、碳酸钡振动流化床干燥机、碳酸钡专用干燥设备生产线环保除尘与安全系统
(一)四级除尘净化工艺
- 一级旋风分离
- CLT/A 型旋风除尘器(进口风速 20-22m/s),分离≥50μm 颗粒,效率≥92%,回收粗粉通过螺旋输送机返回床层;
- 二级滤筒除尘
- 防静电 PTFE 覆膜滤筒(过滤精度 0.5μm,表面电阻率≤1×10?Ω),脉冲反吹压力 0.6MPa,周期 20 秒,粉尘收集效率≥99.9%;
- 三级湿式洗涤
- 填料塔(液气比 0.3L/m3),循环液添加 0.1% 分散剂(如六偏磷酸钠),捕捉≤1μm 颗粒,出口粉尘浓度≤3mg/m3,远低于《大气污染物综合排放标准》(GB 16297-1996);
- 四级活性炭吸附
- 尾气经活性炭吸附床(碘吸附值≥1000mg/g),去除残留微量钡蒸气,确保排放安全性。
(二)安全防护体系
- 毒性防护
- 设备全密闭设计,进出口采用气幕密封(气压 100-150Pa),防止粉尘外溢;
- 操作室配备独立新风系统(换气次数 15 次 /h),安装钡浓度检测仪(量程 0-10mg/m3),超标时自动启动负压抽排。
- 防爆防静电
- 设备接地电阻≤4Ω,所有法兰连接处设置导电跨接(电阻≤0.01Ω);
- 振动电机选用防爆型(Ex IIB T4),粉尘浓度传感器(量程 0-2000mg/m3)实时监测,浓度≥爆炸下限 25% 时自动启动氮气吹扫(流量 15m3/h)。
五、碳酸钡振动流化床干燥机、碳酸钡专用干燥设备生产线智能控制与自动化
(一)PLC+SCADA 控制系统
- 核心功能
- 配方管理:存储 20 组工艺配方(区分微米级 / 纳米级 / 球形碳酸钡),一键切换时间≤1 分钟,包含温度、风速、分散剂用量等 30 + 参数;
- 含水率在线监测:通过微波水分仪(精度 ±0.2%)实时反馈出料含水率,自动调节进料速度与振动频率,实现闭环控制;
- 能耗优化:集成能源管理模块,实时计算单位能耗(蒸汽消耗≤1.0kg/kg 水,电耗≤0.45kW?h/kg 水),超限时自动提示清理换热器积垢。
- 人机界面
- 15 英寸工业级触摸屏,显示流化床三维温度场、振动幅值曲线、除尘系统压差等实时数据;
- 支持历史数据追溯(存储周期≥2 年),可导出干燥曲线、报警记录、维护日志,便于质量追溯与工艺优化。
(二)快速维护与清洁
- 快拆式结构
- 流化床主体分段法兰连接,单段拆卸时间≤20 分钟;分布板采用螺栓快拆设计,配备自动吹扫装置(压缩空气 0.8MPa),10 分钟内完成孔眼清理;
- 集成 CIP 在线清洗系统:50℃温水循环冲洗(流量 10m3/h)15 分钟,继以 0.05% 氢氧化钠溶液消毒(温度 60℃,时间 10 分钟),残留率≤0.01%。
- 维护周期
- 日常:每次停机后吹扫内壁,检查密封件磨损(硅橡胶垫更换周期 3 个月);
- 每周:紧固振动电机地脚螺栓(扭矩 80-100N?m),检测轴承温度(正常≤75℃);
- 每月:校验温度传感器与水分仪(误差 >±1% 时校准),检查氮气管道密封性(压降≤5kPa/10 分钟)。
六、碳酸钡振动流化床干燥机、碳酸钡专用干燥设备生产线应用案例与经济性分析
(一)典型工况运行数据
项目 | 微米级碳酸钡(D50=50μm) | 纳米级碳酸钡(D50=80nm) | 技术优势对比 |
处理量 | 600-1200kg/h | 300-600kg/h | 粉尘排放浓度降低 80% |
进料含水率 | 22% | 18% | 团聚率控制在 8% 以下 |
能耗 | 蒸汽 0.9kg/kg 水 | 导热油 0.4kW?h/kg 水 | 破碎率较传统设备低 60% |
运行时间 | 连续运行 8000 小时无故障 | 年停机维护≤4 次 | 自动化程度提升 50% |
(二)经济性指标
- 投资成本
- 单套设备(处理量 800kg/h)投资约 180-240 万元,包含四级除尘系统、防静电结构、智能控制系统;
- 相比传统箱式干燥设备(投资 120-180 万元),初期成本增加 30%-40%,但生产效率提升 60%,人工成本降低 50%。
- 运行成本
- 以微米级碳酸钡为例,年处理量 10000 吨,年能耗费用(蒸汽 + 电)约 80-100 万元,较滚筒干燥机节省 50 万元 / 年;
- 维护成本:滤筒更换周期 1 年(费用 10 万元 / 次),防静电涂层保养费用≤8 万元 / 年,设备寿命≥10 年。
七、碳酸钡振动流化床干燥机、碳酸钡专用干燥设备生产线技术创新与行业适配
(一)核心技术优势
- 高密度物料流化技术
- 通过风速梯度设计与振动参数优化,实现 4.43g/cm3 高密度碳酸钡的稳定流化,流化风速较传统设备降低 15%,能耗节省 20%。
- 低毒粉尘控制
- 四级除尘系统将粉尘排放浓度控制在 3mg/m3 以下,搭配全密闭气幕密封,确保生产环境安全,符合《工作场所有害因素职业接触限值》(GBZ 2.1-2019)。
- 智能质量追溯
- 集成微波水分仪与高光谱检测仪(可选),实时监控碳酸钡晶型与杂质含量,关键质量指标(含水率、粒度分布)波动≤5%。
(二)适用范围
- 工业级碳酸钡(粒度 10-200 目,含水率≤30%);
- 纳米级碳酸钡(粒度 50-100nm,需搭配分散剂添加系统);
- 产能范围:200-1500kg/h,支持单机定制与多机并联,可提供防爆型(Ex IIB T4)、GMP 洁净型配置,满足电池正极材料、陶瓷釉料、医药中间体等领域需求。
八、碳酸钡振动流化床干燥机、碳酸钡专用干燥设备生产线结语
本方案针对碳酸钡的高密度、易静电团聚及毒性特性,构建了以耐磨防静电结构、高效除尘系统、智能控制为核心的干燥解决方案。通过低温稳定流化、四级净化工艺与自动化管理,实现了安全、高效、环保的干燥过程,适用于不同粒度等级的碳酸钡生产。设备支持定制化设计,可根据客户产能、杂质控制要求及特殊行业标准(如医药、食品级)提供针对性配置,助力提升产品质量与生产安全性。
振动流化床现场实拍图:
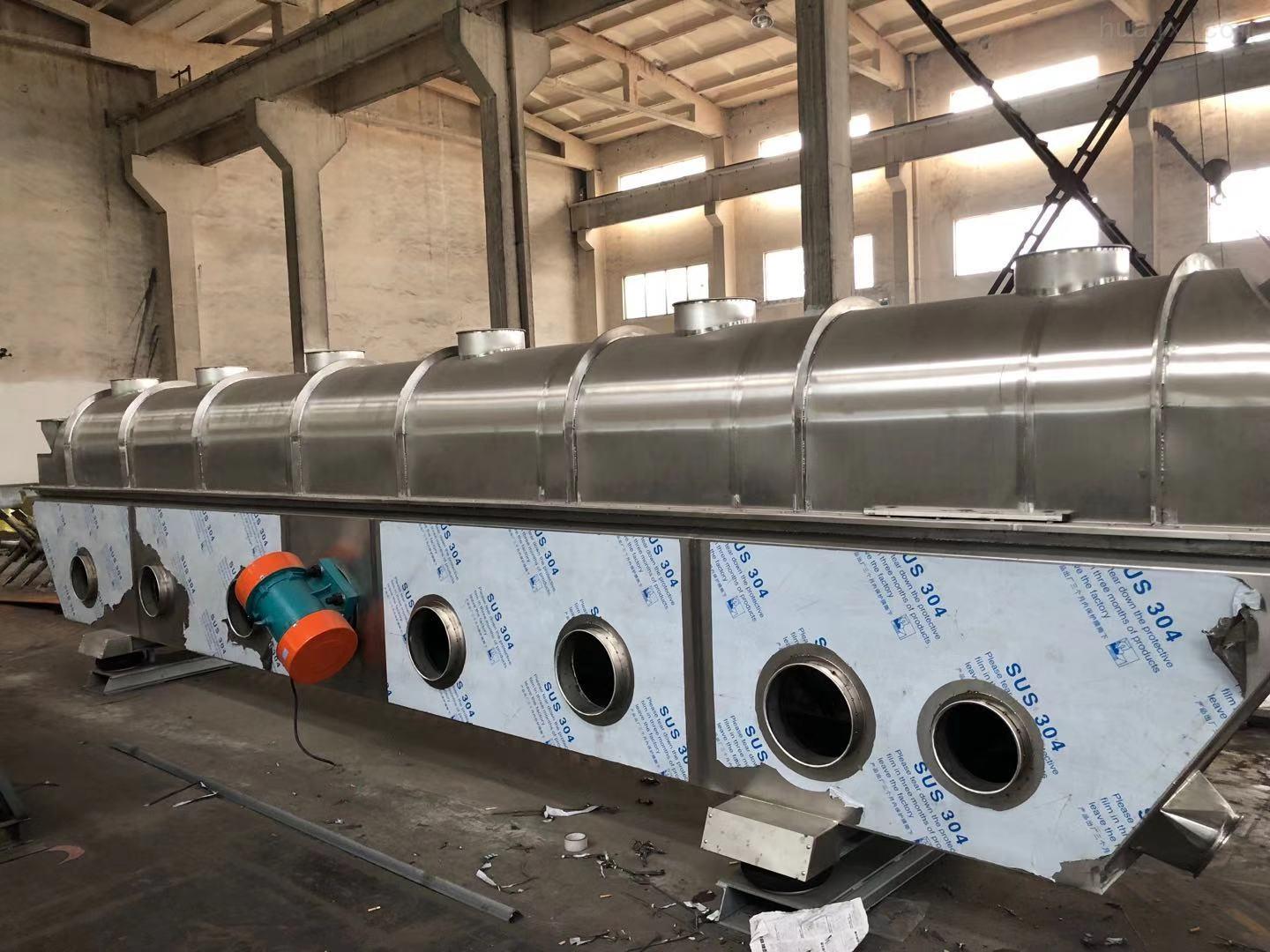